Pneumatic gripper
Introduction to pneumatic grippers
A gripper is a motion device that mimics the movements of people, in the case of the gripper, it is the fingers. A gripper is a d
evice that holds an object so it can be manipulated. It has the ability to hold and release an object while some action is being performed.
The fingers are not part of the gripper, they are specialized custom tooling used to grip the object and are referred to as "jaws." Two main types
of action are performed by grippers:
External: This is the most popular method of holding objects, it is the most simplistic and it requires the shortest stroke length. When the
gripper jaws close, the closing force of the gripper holds that object.
Internal: In some applications, the object geometry or the need to access the exterior of the object will require that the object is
held from the center. In this case the opening force of the gripper will be holding the object.
Learn more about Pneumatic gripper
How does a gripper work?
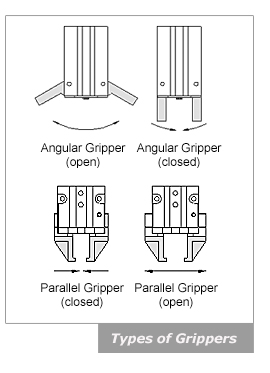
The most widely used gripper is the pneumatically powered gripper; it is basically a cylinder that operates on compressed air. When the air is
supplied, the gripper jaws will close on an object and firmly hold the object while some operation is performed, and when the air direction is
changed, the gripper will release the object. Typical uses are to change orientation or to move an object as in a pick-n-place operation.
Types of Pneumatic Grippers
The most popular types of pneumatic grippers are the 2 jaw parallel and 2 jaw angular gripper styles. Parallel grippers open and close parallel
to the object that it will be holding, these are the most widely used grippers. They are the simplest to tool and can compensate for some
dimensional variation. Angular grippers move the jaws in a radial manner to rotate the jaws away from the object and therefore require more space.
There are also 3 jaw and toggle style grippers that are designs for more specific handling requirements.
Gripper Force
Grippers have a force rating that is referenced with an air pressure. The force of a gripper is influenced by the air pressure, if you increase
the air pressure by 20% then you have increased the force on the griper by 20% (up to the gripper maximum air pressure rating). This also gives
you the ability to reduce the gripper force by using an air regulator.
Major Factors in Choosing a Pneumatic Gripper and Jaw Design:
When choosing a pneumatic gripper and jaw design, these ate the major factors to consider:
- Part shape, orientation and dimensional variation
If the object has two opposing flat surfaces, then 2 jaw parallel gripper is desired since it can handle some dimensional variation.
Jaws can also be designed to handle cylindrical objects with the 2 jaw concept. Keep in mind that a retention or encompassing grip requires much less force.
How to choose a Pneumatic Gripper
- Part shape, orientation and dimensional variation
- Part Weight
- Accessibility
- Environmental
- Retention of the Object
- Part Weight
Grip force must be adequate to secure the object while a desired operation is performed on the object. The type of jaw design must be part of
the force requirement. Keep in mind that you should add a safety factor to the amount of force that you select and air pressure is a factor to
keep in mind.
- Accessibility
This applies both to the work being performed on the object and the amount of room for the gripper jaws. If the work is to the exterior of
the object then it may require an internal grip. Angular grippers are usually less expensive but require additional space for jaw movement.
- Environmental
Harsh environment or clean room applications require grippers designed for those purposes.
- Retention of the Object
When air pressure is lost, the gripper will relax its grip on the object and the object may be dropped. There are spring assist grippers
designed for this type application.
Choose the right gripper for your automated process
Pneumatic Parallel Grippers
A parallel gripper opens and closes parallel to the object that
it will be holding. These are the most widely used grippers. They are the simplest to tool and can compensate for some dimensional variation.
Pneumatic Angular Grippers
An Angular gripper moves the jaws in a radial manner to rotate the
jaws away from the object. This allows for the jaws to move completely away from the object. The object may also be fed directly into the jaws
and possibly eliminate one additional motion.
Pneumatic Grippers for Clean Room & Harsh Environments
A pneumatic gripper for harsh environments is constructed with clean room
grade grease and are equipped with shielding to protect the moving components from particulate.
External components are made of corrosion resistant materials for resistance to de-ionized water or for use in FDA and medical applications.
They also have a scavenge/purge port to be used with vacuum in clean room applications and air supply to keep particulate away from jaws.
Frequently Asked Questions
How to Choose a Jaw Configuration?
The jaws are custom tooling designed to securely hold the object at task. They will make contact with the object and much thought
needs to go into the correct jaw design because it will have a major factor in the force requirement of the gripper.
There are two types of gripping actions:
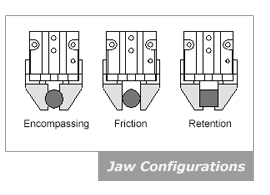
Friction:
Friction gripping jaws rely completely on the force of the gripper to hold the object, they are the easiest to fabricate and may require
more force to hold the object. This is especially true for objects that do not have flat surfaces. Parts can be dislodged by forces applied
from any direction.
Retention or Encompassing:
Retention or encompassing gripping jaws will hold the object and cradle it in the jaws. It is the preferred method since it adds stability
to holding the object and requires less force to hold the object, to drop the object you must overcome the force to open the jaws. Keep in
mind that the travel stroke of the gripper may have to be increased to encompass the object. If the jaw encompasses the object 1/16" on both
sides, then the stroke length requirement will need to be increased by 1/8".
Gripper | Related Products
↓ View this page in another language or region ↓