A Solenoid valve is used wherever fluid flow has to be controlled automatically. They are being used to an increasing degree in the most varied types of plants and equipment. The variety of different designs which are available enables a valve to be selected to specifically suit the application in question.
How is a solenoid operated valve being made?
There are 5 main parameters to
consider when selecting a valve:
- Cv
- media compatibility
- pressure
- temperature
- process fitting
Solenoid valve is a control units which, when electrically energized or de-energized, either shut off or allow fluid flow. The actuator takes the form of an electromagnet. When energized, a magnetic field builds up which pulls a plunger or pivoted armature against the action of a spring. When de-energized, the plunger or pivoted armature is returned to its original position by the spring action.
How does a solenoid valve operate?
To the mode of actuation, a distinction is made between direct- valves, internally piloted valves, and externally piloted valves. A further distinguishing feature is the number of port connections or the number of flow paths ("ways").
Direct-acting solenoid valve
With a direct-acting solenoid valve, the seat seal is attached to the solenoid core. In the de-energized condition, a seat orifice is closed, which opens when the valve is energized.
Direct-acting 2-way solenoid valve
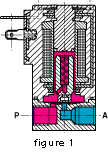
Two-way solenoid operated valves are shut-off valves with one inlet port and one outlet
port (Fig. 1). In the de-energized condition, the core spring,
assisted by the fluid pressure, holds the valve seal on the valve
seat to shut off the flow. When energized, the core and seal are
pulled into the solenoid coil and the valve opens. The electro-magnetic
force is greater than the combined spring force and the static
and dynamic pressure forces of the medium.
Direct-acting 3-way solenoid valve
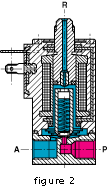
Three-way solenoid operated valves have three port connections and two valve seats. One valve
seal always remains open and the other closed in the de-energized
mode. When the coil is energized, the mode reverses. The 3-way solenoid valve shown in Fig. 2 is designed with a plunger type core. Various
valve operations can be obtained according to how the fluid medium
is connected to the working ports in Fig. 2. The fluid pressure
builds up under the valve seat. With the solenoid coil de-energized, a
conical spring holds the lower core seal tightly against the valve
seat and shuts off the fluid flow. Port A is exhausted through
R. When the coil is energized the core is pulled in, the valve
seat at Port R is sealed off by the spring-loaded upper core seal.
The fluid medium now flows from P to A.
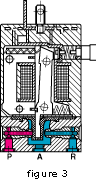
Unlike
the versions with plunger-type cores, pivoted-armature valves
have all port connections in the valve body. An isolating diaphragm
ensures that the fluid medium does not come into contact with
the solenoid coil chamber. Pivoted-armature valves can be used to obtain
any 3-way valve operation. The basic design principle is shown
in Fig. 3. Pivoted-armature valves are provided with manual override
as a standard feature.
Internally piloted solenoid valve
With
direct-acting valves, the static pressure forces increase with
increasing orifice diameter which means that the magnetic forces,
required to overcome the pressure forces, become correspondingly
larger. Internally piloted solenoid valves are therefore employed
for switching higher pressures in conjunction with larger orifice
sizes; in this case, the differential fluid pressure performs
the main work in opening and closing the valve.
Internally piloted 2-way solenoid valve
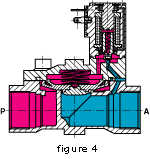
Internally piloted solenoid valves are fitted with either a 2-
or 3-way solenoid valve. A diaphragm or a piston provides
the seal for the main valve seat. The operation of such a valve
is indicated in Fig. 4. When the pilot valve is closed, the fluid
pressure builds up on both sides of the diaphragm via a bleed
orifice. As long as there is a pressure differential between the
inlet and outlet ports, a shut-off force is available by virtue
of the larger effective area on the top of the diaphragm. When
the pilot valve is opened, the pressure is relieved from the upper
side of the diaphragm. The greater effective net pressure force
from below now raises the diaphragm and opens the valve. In general,
internally piloted valves require a minimum pressure differential
to ensure satisfactory opening and closing. Omega also offers
internally piloted valves, designed with a coupled core and diaphragm
that operate at zero pressure differential (Fig. 5).
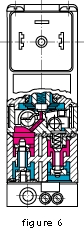
Internally piloted multi-way solenoid valve
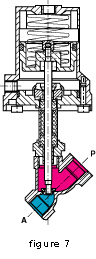
Internally
piloted 4-way solenoid valves are used mainly in hydraulic and
pneumatic applications to actuate double-acting cylinders. These
valves have four port connections: a pressure inlet P, two cylinder
port connections A and B, and one exhaust port connection R. An
internally piloted 4/2-way poppet valve is shown in Fig. 6. When
de-energized, the pilot valve opens at the connection from the
pressure inlet to the pilot channel. Both poppets in the main
valve are now pressurized and switch over. Now port connection
P is connected to A, and B can exhaust via a second restrictor
through R.
Externally piloted solenoid valve
With
these types an independent pilot medium is used to actuate the
valve. Fig. 7 shows a piston-operated angle-seat valve with closure
spring. In the unpressurized condition, the valve seat is closed.
A 3-way solenoid valve, which can be mounted on the actuator,
controls the independent pilot medium. When the solenoid operated valve
is energized, the piston is raised against the action of the spring
and the valve opens. A normally-open valve version can be obtained
if the spring is placed on the opposite side of the actuator piston.
In these cases, the independent pilot medium is connected to the
top of the actuator. Double-acting versions controlled by 4/2-way
valves do not contain any spring.
How to select a Solenoid valve for process applications